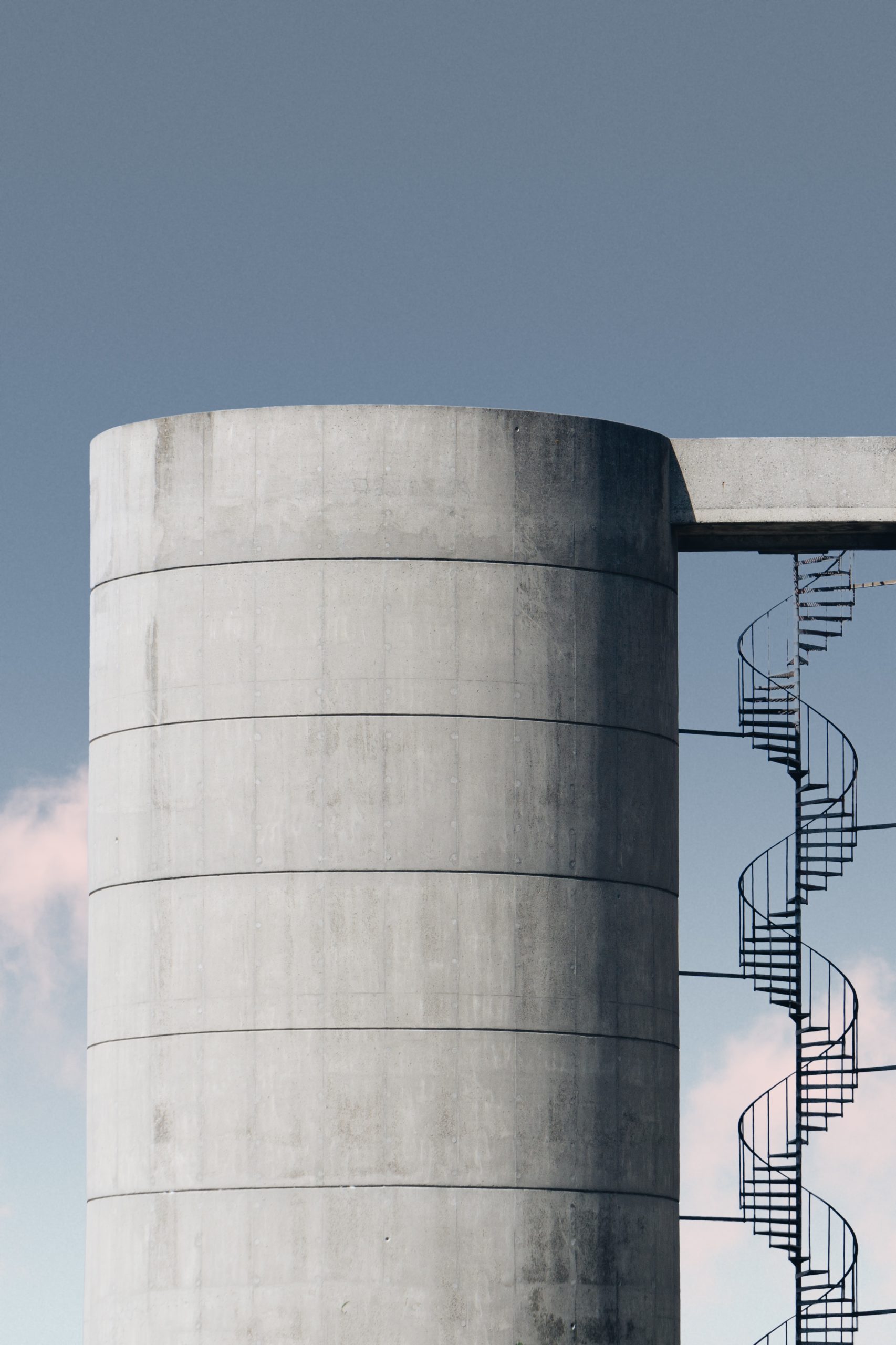
Cement production alone is responsible for about 8% of global carbon dioxide emissions—that’s a lot. If cement were its own country, it would be the third largest emitter after China and the United States. But much of our modern world heavily relies on the material. Most of the buildings, bridges, roads and dams would quite literally collapse without it. So, what can we do?
“If we aim to achieve net-zero by 2050 and limit global warming to 1.5ºC,” says Leah Ellis, Ph.D. (Co-Founder & CEO at Sublime Systems), “we must eliminate cement’s CO2 emissions.” But we also “must keep building if we are to shelter the world’s growing and urbanizing human population. It is estimated that 70% of the infrastructure that will exist in 2050 is not yet built.”
Ellis and Prof. Yet-Ming Chiang founded Sublime Systems in 2020, which is behind a new technology making decarbonized cement (Sublime Cement™) without fossil fuel or limestone. They have replaced the industry’s energy-intensive kilns with an electrochemical process using renewable energy. Sublime’s pilot plant in Somerville, Massachusetts is capable of producing 100 tons of decarbonized cement annually, and with a recent $40M in funding, they are building a demonstration-scale plant capable of producing up to 40,000 tons per year—enough to meet the minimum quantity needed for ready-mix concrete suppliers. —Charlotte DeFazio
How does Sublime Systems’ technology work?
Sublime Systems is commercializing breakthrough technology to produce low-carbon cement that performs like the cement society depends on, without the environmental cost. Sublime replaces the industry’s legacy kilns—the most energy and fossil-fuel-intensive part of the traditional cement manufacturing process—with an electrochemical process that makes cement at an ambient temperature. Sublime’s proprietary process uses renewable electricity instead of fossil fuels to extract calcium and silicates from raw materials to make cement, avoiding both CO2 process emissions and heating emissions. The company can do this with a diversity of raw materials as its process is not limited to the carbonate minerals needed to make today’s cement. The resulting Sublime Cement™ is a drop-in replacement for today’s carbon-intensive Portland cement.
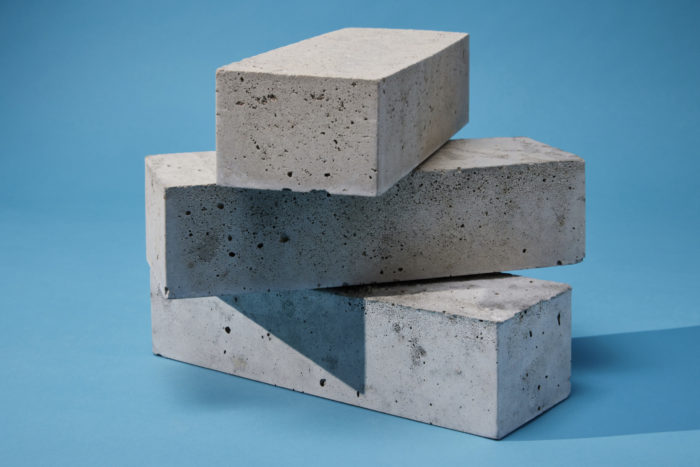
Is the main problem with standard concrete due to the manufacturing process of cement?
Yes, cement is the key ingredient in concrete and the cement-making process is the largest source of industrial CO2 emissions. Today’s cement production involves the use of coal-fired kilns, where limestone (calcium carbonate) is subjected to thermal decomposition and sintered with silicate to create Portland cement. This manufacturing process requires extremely high temperatures, exceeding 1400°C, which are generally achieved by burning coal or gas. In addition to the emissions from the fuel needed to reach that high temperature, the limestone releases nearly half its weight as CO2 when it decomposes into lime—a key step in cement production.
Cement is responsible for 8% of global carbon dioxide emissions, but it is also a vital material that forms the literal foundation of our society. If cement were a country, it would be the third largest emitter after China and the US. If we aim to achieve net-zero by 2050 and limit global warming to 1.5°C, we must eliminate cement’s CO2 emissions. However, at the same time, we must keep building if we are to shelter the world’s growing and urbanizing human population. It is estimated that 70% of the infrastructure that will exist in 2050 is not yet built. We need cement now more than ever—therefore, we need a breakthrough approach to low-carbon cement production. Sublime is answering the call with a breakthrough approach to avoid—not capture—CO2 emissions from limestone and fossil fuels while producing a cement that meets the needs of ready-mix concrete producers so we can keep building.
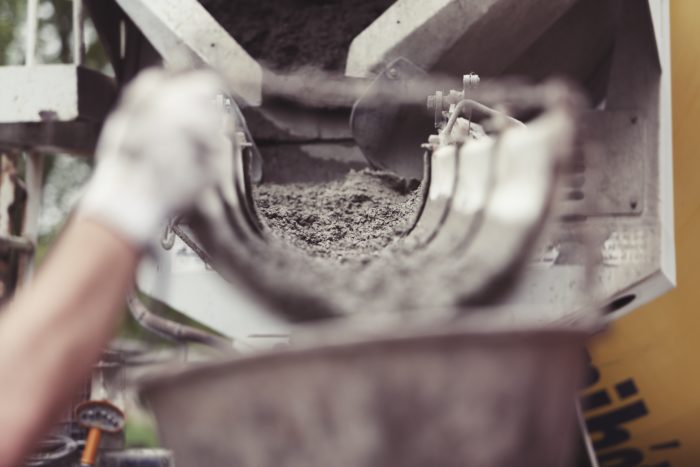
What are the largest challenges in getting the industry to fully adopt carbon neutral concrete?
The cement and concrete industry faces several significant challenges in fully adopting decarbonized concrete. One major challenge is the limited availability of green fuels that can provide the high temperatures required in cement production. Additionally, avoiding direct emissions from limestone decomposition requires expensive equipment replacements. Carbon capture and sequestration from cement kilns doubles the capital expenditure and the cost of cement and has significant logistical and geographic challenges. Sublime’s electrochemical process avoids both the CO2 process emissions and the heating emissions and is on track to reduce over 90 percent of cement’s carbon emissions.
Skepticism is another hurdle to be addressed. Above all else, buyers want a product that matches the performance of conventional concrete made with ordinary Portland cement. Our solution completely re-imagines the cement-making process yet still produces a frictionless replacement that is chemically identical to today’s hardened concrete. Sublime has conducted extensive testing to demonstrate that our cement meets or exceeds various industry standards, including strength, flow rate, set time, and durability. Furthermore, Sublime’s process offers the advantage of using multiple feedstocks, which can help mitigate the environmental impact of mining. By selecting minerals like calcium or byproducts from other mines, the process can mitigate the effects of mining on local environments.
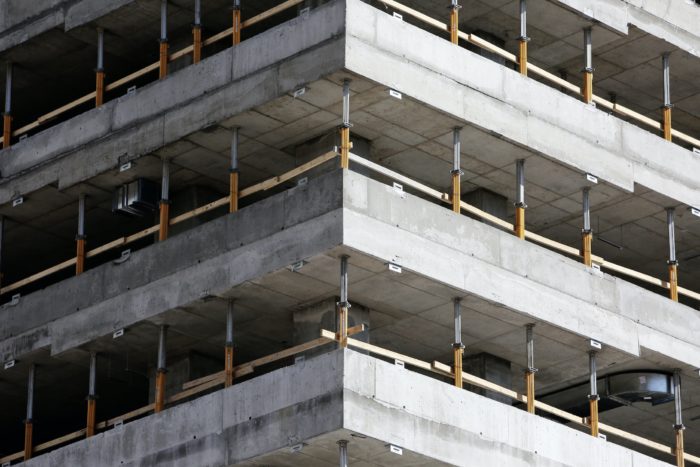
In 2020, the Global Cement and Concrete Association announced its Climate Ambition to achieve carbon neutral concrete around the world by 2050. How optimistic are you that this goal will be met?
There is strong reason for optimism in achieving the goal of carbon neutral concrete by 2050. We have to decarbonize the cement and concrete industry if we expect to effectively combat global climate change and mitigate its worst impacts on society. To reach this goal, integrating decarbonization solutions into existing supply chains without significant cost premiums is crucial. As population growth and economic development continue, the demand for cement will only increase. It is estimated that the Earth’s floor area will double by 2060—a rate of construction equivalent to building a new city the size of Houston every 20 days. Growing interest from leaders in the cement and construction industries, including strategic investors like Siam Cement Group (SCG), demonstrates an increasing commitment to global decarbonization. However, performance, price, and scalability remain critical factors that need to be proven before widespread adoption.
Collaboration within industry and global initiatives such as the GCCA’s Climate Ambition hold immense potential in catalyzing deep decarbonization efforts. It is encouraging to witness governments removing obstacles for decarbonization and countries competing to become leaders in the sustainable industrial revolution. However, the commercialization of carbon neutral concrete requires a mix of public-private partnerships to provide the right expertise, risk oversight, and to accelerate the adoption of new technologies.
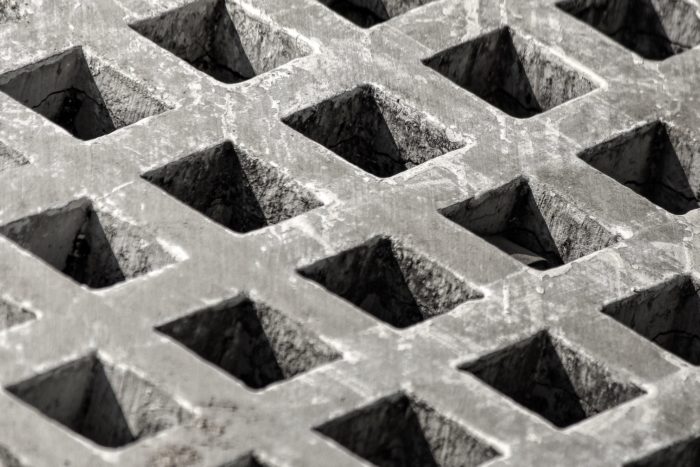
How does Sublime Systems compare with other eco-friendly concretes on the market?
Sublime Systems differentiates itself from other eco-friendly concretes on the market through its unique process. Unlike alternative options, Sublime’s process can produce industry-accepted, ASTM-compliant cement without using fossil fuels or limestone. This eliminates the need for additional energy, cost, and complexity associated with carbon capture and storage.
Are there other sustainable building materials on the rise that you are interested in or inspired by?
Sublime Systems draws its inspiration from Roman cement, which was used in the construction of cities and roads in ancient Rome. Similar to Roman cement, Sublime Cement™ is a highly engineered material that exhibits high ultimate strength and exceptional durability.
What are your thoughts on recycling concrete waste?
Recycling concrete waste is essential to decarbonizing the cement and concrete industry, especially considering the mass of buildings is now estimated to surpass the mass of all living things on Earth. At Sublime, we recognize the need to recycle as much concrete as possible if we are to minimize our footprint on the Earth’s natural beauty and ecosystems. Our technology enables us to utilize waste cement and demolition dust as inputs in the cement-making process.
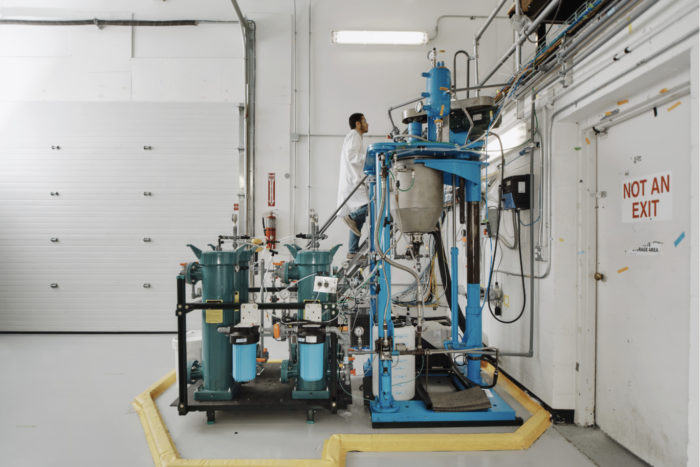
What makes “green concrete” sustainable in the long-term?
The long-term sustainability of “green concrete” hinges on the cement-making technologies that avoid CO2 emissions, rather than those that rely on CO2 capture. We call these technologies true-zero, not net-zero, which implies some addition and subtraction to reach zero. These transformative carbon-avoidance technologies decarbonize without the added capital expenditure, water, energy, and land required for carbon capture, and without the logistical complexities of carbon sequestration.
To use a metaphor, carbon capture is a mop for cleaning up greenhouse gas pollution, whereas carbon avoidance is a direct and permanent solution—one that pushes the frontier of technology while establishing a platform for generations of innovations and enhancements. While both carbon avoidance and carbon capture technologies are essential and urgently needed, governments and investors must prioritize funding for avoidance technologies. This approach not only achieves immediate pollution reduction but also establishes avoidance technologies as the mainstream solutions for the future.
In a post-carbon world, even a thousand years from now, our descendants will remember our era as the pivotal time when their sustainable industry took root.
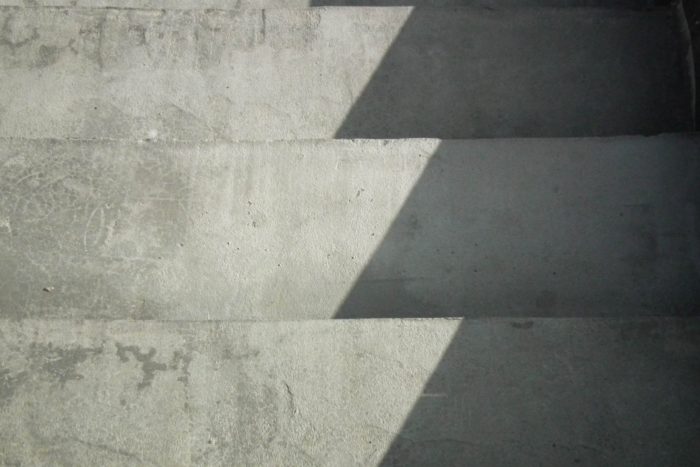
Any advice for people seeking environmentally conscious builders and building materials?
A simple but impactful step is to ask for low-carbon concrete. Just requesting, even if nothing else, puts pressure on the supply chain and raises awareness. Additionally, consider paying a small premium for low-carbon cement. While cement is one of the cheapest and most carbon-intensive materials, paying a modest price premium can have a tremendous carbon impact, surpassing the benefits of other clean technologies like sustainable aviation fuel.
How are things going with your pilot plant?
Sublime Systems has successfully demonstrated the viability and scalability of its approach. Our pilot plant can produce cement at a rate of 100 tonnes per year and has been running for several hundred hours continuously. Our business model is to sell cement to ready-mix concrete producers. Ultimately, Sublime may consider a licensing model in order to have a swift and massive impact on global CO2 emissions.
We recently raised a $40M Series A to ramp up production at our pilot plant, conduct product testing with customers, secure offtake agreements, and prepare for the construction of a larger plant. With this funding, Sublime will build a demonstration-scale plant capable of producing up to 40,000 tonnes of cement per year, which is expected to be commissioned by 2025. At that point, we will be able to fill silos with our cement, which is the minimum quantity needed for ready-mix concrete suppliers to start using Sublime Cement™ commercially.
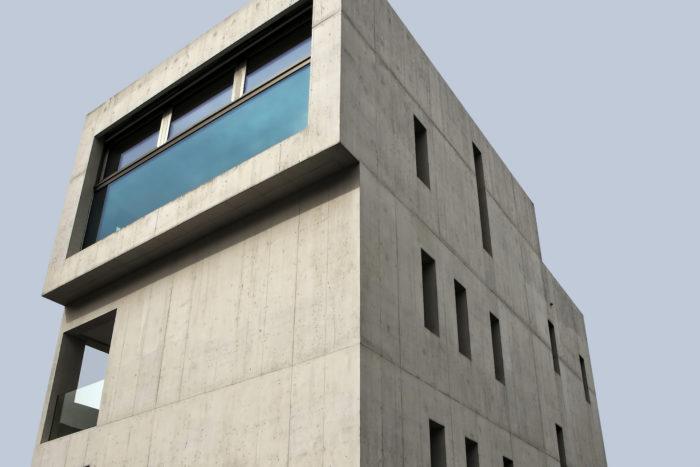