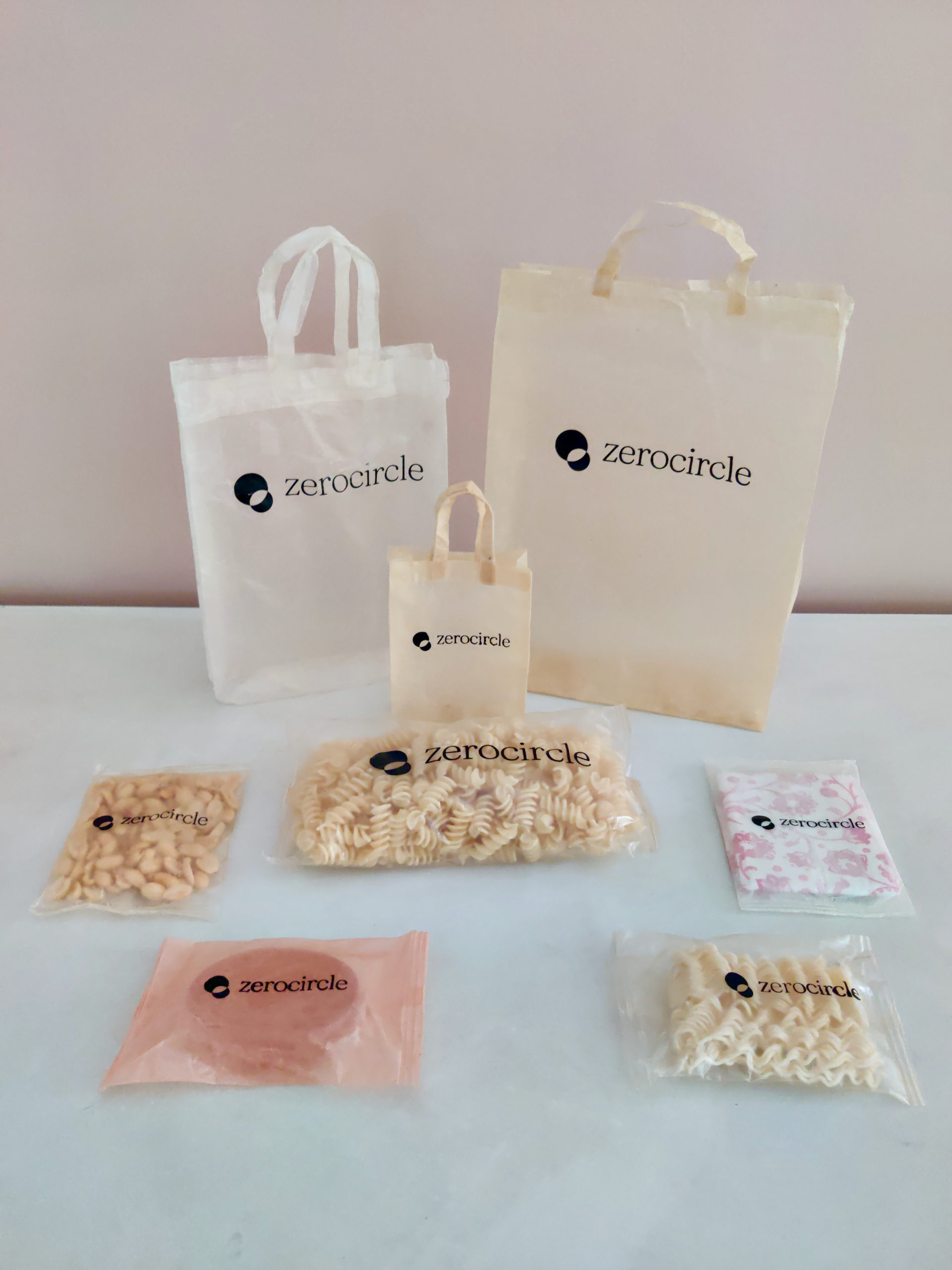
Over the course of one week, even one day, take note of where you see thin-film plastic: bags, food wrapping, dry cleaning, packaging, etc. It’s an exhaustive list and what we see in our day-to-day only scratches the surface of the problem. Plastic films make up around 46% of all ocean plastic leakage. Earlier this year, the Tom Ford Plastic Innovation Prize (powered by Lonely Whale) announced its 8 finalists for thin-film alternatives, which brands like Nike, HP, and Stella McCartney are now testing in their supply chains. The Clean Seas Research Program at the Seattle Aquarium is also analyzing the product degradation rates in temperate waters and in a simulated whale gut (!). We caught up with one of the finalists, Zerocircle, a biotech company based in India where they sustainably source seaweed from coastal communities to make thin-film plastic alternatives. —Charlotte DeFazio
What first inspired you to enter this work?
Over the years, I realized that any changes I formulated as an individual made little impact on the rising waste problem and changing climate. During that time, a large part of the global tech ecosystem was involved in data collection and product modeling that helped improve energy efficiencies. It made sense. Since I came from a tech background, I thought it could be a way to contribute. I decided to help companies build IoT-based solutions to reduce their carbon footprint. However, while there was enough data driven technology, the issue at hand was to use this data to improve the circularity of materials in manufacturing. One of the biggest culprits was materials and the impossible recycling economics attached to it. This gap pushed me to innovate with bio-materials, and that motivated me to research resources that help minimize overall environmental impact. I was ecstatic when I discovered seaweed. It was an answer to the problem of finding sustainable material sources and a model that could be scaled globally.
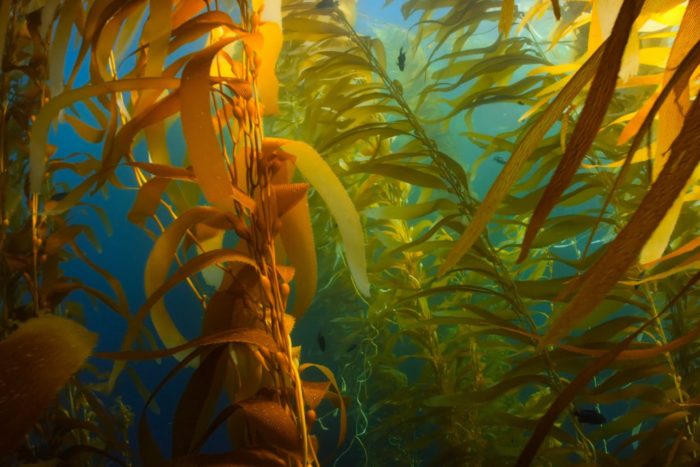
Where does your seaweed come from and who is harvesting it?
Currently, our raw material is sourced from locals in the coastal and fishing communities that are open to the idea of secondary livelihood opportunities. There are a few NGOs who are involved in training and assisting the locals with cultivation techniques and seedling material. We have also seen an emerging interest from sea-entrepreneurs who were traditionally involved in aquaculture and their generation is exploring new avenues. We ensure that we work with people who are farming the seaweed and not plucking it from the wild.
From planting to finished product, how long does your process take?
A typical growth cycle could vary depending on the species, however it would take an average of 30-45 days for it to grow from seedling to being ready for harvest. The harvest is then sun-dried for a day or two depending on the weather conditions and then sent for processing. The processing of this material from extraction to conversion would take less than a day. But these processes are dependent on how close we set up our processing units to the site of cultivation.
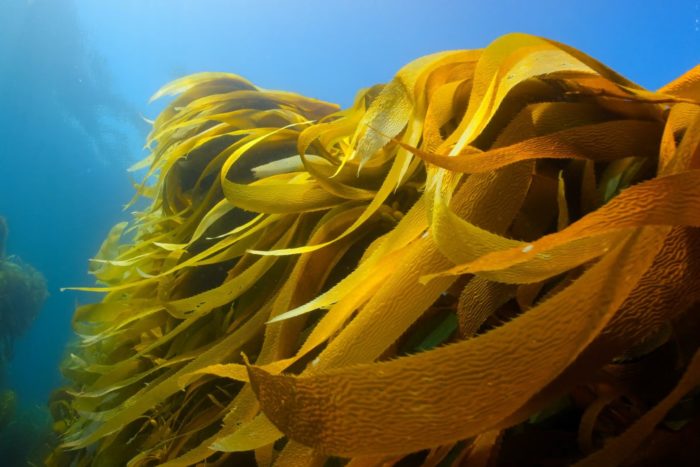
How much energy is used in production?
Our current numbers are rough estimates of the possible energy consumption at commercial scale. There’s an enormous amount of energy required to convert oil into a plastic pellet. It is responsible for approximately 60% of the emissions in the life cycle of plastics. We estimate we can reduce up to 80% of those emissions at scale.
What are the economic differences for companies to make the switch from conventional plastic products to yours?
Based on our estimates, we will be able to match the pricing of food-grade paper. The advantage over it is obvious, it is tree-free and see-through (clear).
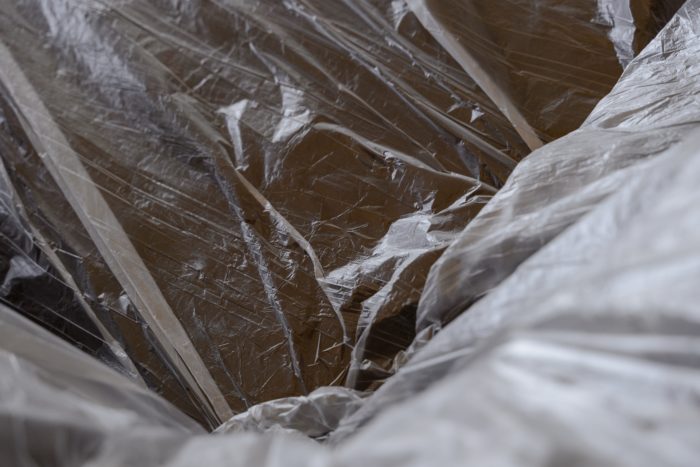
Do you support mycelial materials?
Mycelium is a great resource for making materials and provides a great alternative for rigid packaging. In the future, we would love to collaborate with companies to jointly create something unique in the space.
Will your current production model be able to keep up with demand? How are you helping partners scale up for commercial production?
We are at a pre-commercial stage. We hope to launch our commercial production by the end of year through our demonstration commercial site. As the next year progresses, we will be licensing the technology to existing players so we can produce and scale faster to meet the demand of our customers.
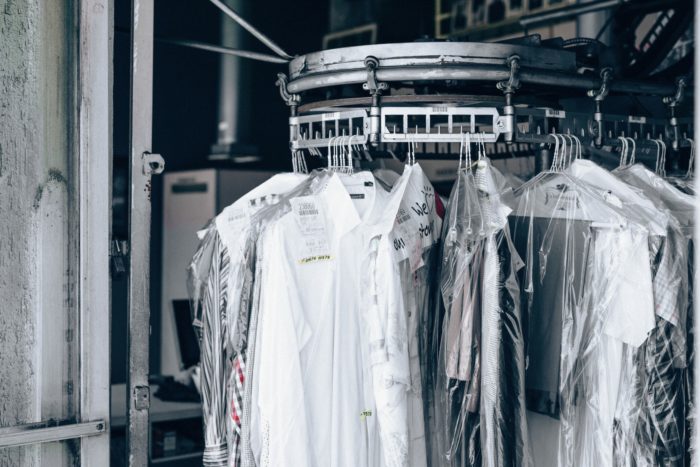
Where could your flexible films be used in the fashion industry?
Just in the textile space, there are several places where single-use plastics are used in huge quantities. The most visible part of it is seen at the point of sale with the polybags or shopping bags handed to customers. However, there is a greater requirement at the back-end. A large part of the global textile industry moves materials from east to west, either in the form of complete apparels or unstitched goods. Storage of individual items in shipping containers is important to keep them dust-free and fresh. Then there’s the long warehousing of these apparels in stores or distribution centers. But we continue using packaging to maintain these materials. For example, your dry cleaning and laundry services also use flexible films to keep clothes dust- and lint-free.