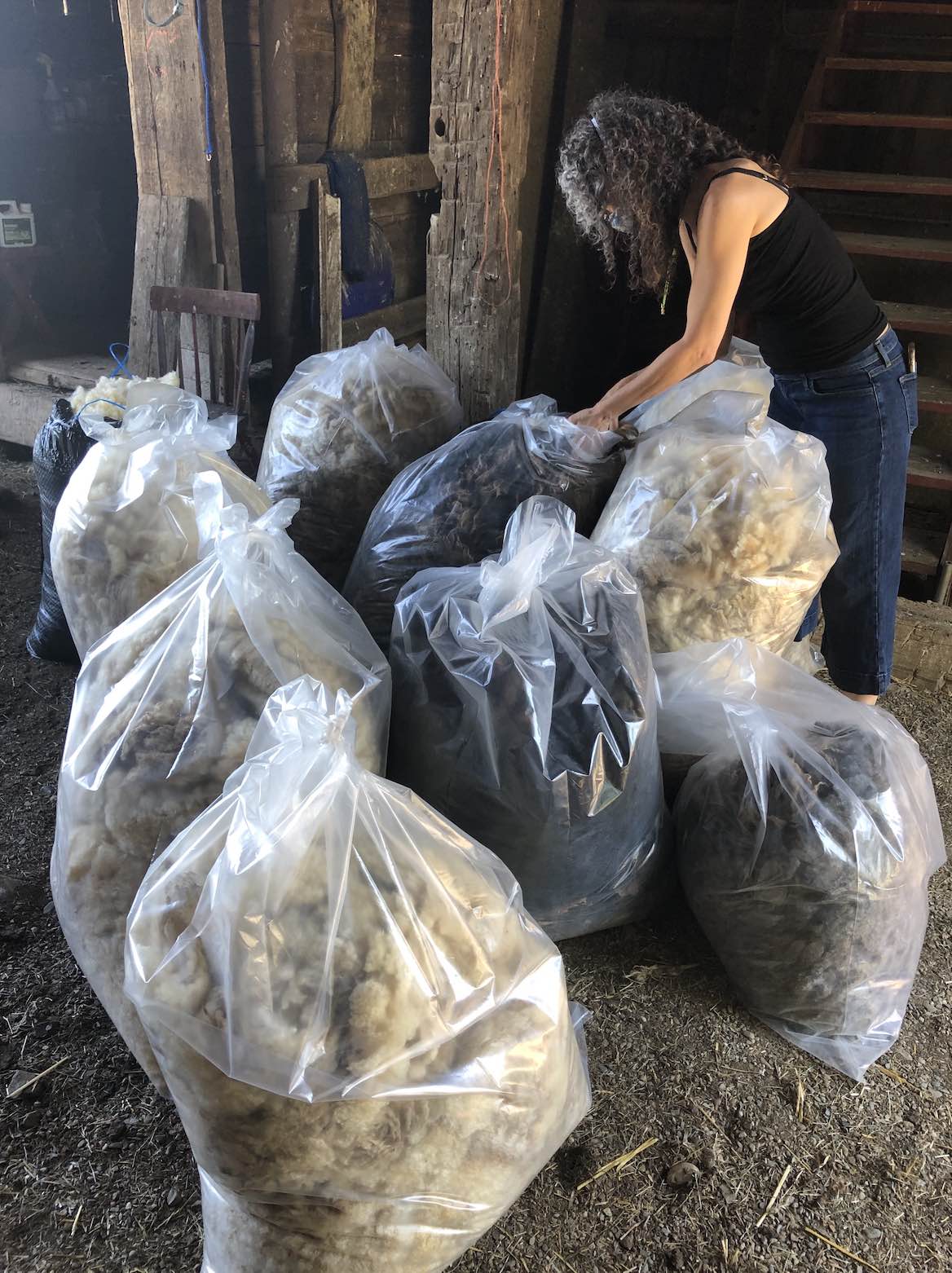
New York Textile Lab is a burgeoning design and consulting company with a vision to move the design industry away from extracting and exploiting Earth’s resources, and towards implementing nature-based, regenerative practices. Founder Laura Sansone, a textile designer and Assistant Professor of textiles at Parsons The New School for Design, has been connecting New York designers (apparel, product, interior) with fiber farmers who share a deep commitment to biodegradable materials and regenerative farming. The farms are also all within 300 miles of New York City, where the Textile Lab has run classes with natural dyeing, composting waste, creating products from used clothing and more. This year, they launched an application process for farms to join called the Carbon Farm Network, and are working on an app that will help independent designers connect directly to the region’s resources, so “they can make their own yarns starting with the soil where the fibers originate.” —Jane Ratcliffe
What led you to founding New York Textile Lab?
I moved to the Hudson Valley in 2003 to live on a farm where I had a textile studio. At that time, I was interested in practicing soil to soil production methods with my textile products—I wanted whatever I made to be able to be composted and returned to the soil. I started working with natural dyes, many I extracted from plants on the farm, to color and print on organic cotton textiles.
The lands in the Hudson Valley and Catskills are the watershed for the rivers, streams and reservoirs that provide water to the 9 million people in NYC. I realized that the health and stewardship of the soil upstate was really important, not only to those in the Hudson Valley, but also to the people who live in NYC. Also, the densely populated area of NYC is really important to the economy of the upstate farms. I thought “If I can have traceability and transparency with the locally grown food that I eat, why can’t I have the same experience with my textile products?” I decided to run my textile design classes at the Union Square Greenmarket. I received a grant from Parsons to build a Textile Lab, a mobile kitchen and workstation to allow us to harvest for dye materials at the market and create textiles (by hand) with the yarn and wool roving being sold there. I worked with students to create dyes and we composted our dye and textile waste at the composting station there. We also partnered with Wearable Collections, a used clothing service that has a clothing drop off area at the Greenmarket. My students addressed circular design concepts; creating products from used clothing that they dyed with local plants, sometimes blending their creations with the local fiber resources. The idea of small interdependent market systems began to take shape in my mind, and my design and consulting business grew.
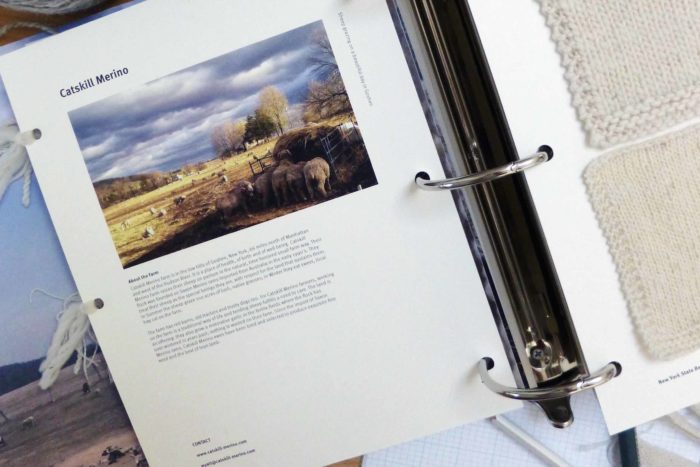
What’s the difference between extracted resources and regenerative ones?
Any resource that human beings remove from Earth is extracted. As humans, we have constructed a false narrative about our relationship to nature and her resources. We position ourselves as having the right and duty to commodify almost everything that the earth provides through boundless extraction. Regenerative resources are those that can be removed from the earth and through a combination of human and natural interventions, can return to the earth so that natural systems aren’t depleted. From a textile design perspective, we should divest from materials that are heavily reliant on fossil fuel extraction, like synthetic polyester and nylon materials. These materials also add to the growing microplastic crisis that is emerging, where we’re finding plastic in our food and bodies. Natural fibers can be grown in regenerative ways by addressing the health of the soils where they’re cultivated. This is true for both plant fibers like cotton, linen and hemp as well as animal fibers like wool. Regenerative farming practices can ensure that the farms where the fibers are being cultivated are using best management practices such as composting protocols, rotational grazing, cover cropping, etc.
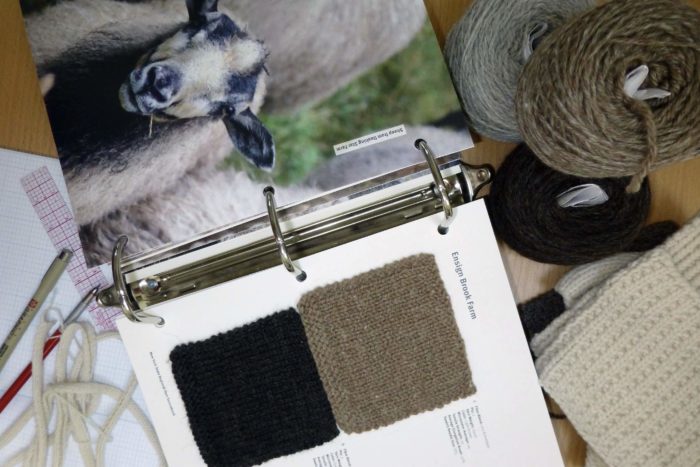
How are you connecting designers directly to farmers, mills and manufacturers?
The most important mission to the work that I do is to bring designers to the beginning of the textile and clothing value chain so they can connect directly to their fiber resources. Often, textile designers don’t enter the value chain until they’re purchasing yarn from a distributer or sometimes, designers don’t even connect with their materials until they are purchasing fabric. Designers are problem solvers, and it doesn’t make sense to enter the value chain in the middle when there are so many opportunities for environmental and economic interventions along the way. When designers engage with their resources at the beginning of the value chain, they can track their materials and connect directly with farms, mills and manufacturers. This gives designers agency and transparency throughout the process. Three years ago, I developed a project with a researcher named Helen Trejo from Cornell University. We created an industry sourcebook called the NYS Regional Yarn Sourcebook. This book contains 72 samples from just a handful of farms in the Hudson Valley. It represents the diversity of fibers that are available as well as information about the farms and the mills.
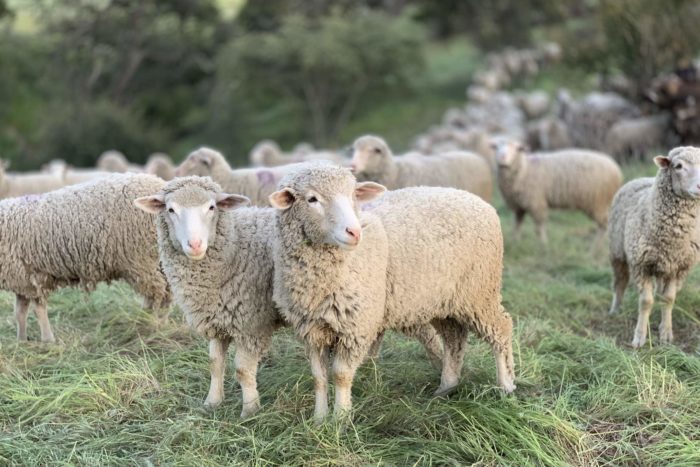
What kind of shearing practices are implemented on the farms you work with?
Shearing is a necessary and benign maintenance measure for sheep and other fiber producing animals. Abuses and violent activities occur in the larger, centralized farming operations where profit is the only motive and where there is a lack of transparency and accountability within the supply chain. None of the farms I work with are cruel to their animals in any way. I work in a bio regional network where the farmers know each other, and often work with the same shearers. When you operate in smaller, decentralized networks, the agents who are involved (farmers, shearers, designers, mill owners, manufacturers) can build trust with each other and develop ‘reputational currency’. Since we’re all part of the same regional network, we rely on each other for our livelihoods. There is more of an incentive to care for the animals, the land and ultimately for each other. I’ve participated in the shearing events at a few different farms in the Hudson Valley, and I’ve never seen any animals severely hurt from the shearing tools, which for lack of a better description, resemble large electric shavers.
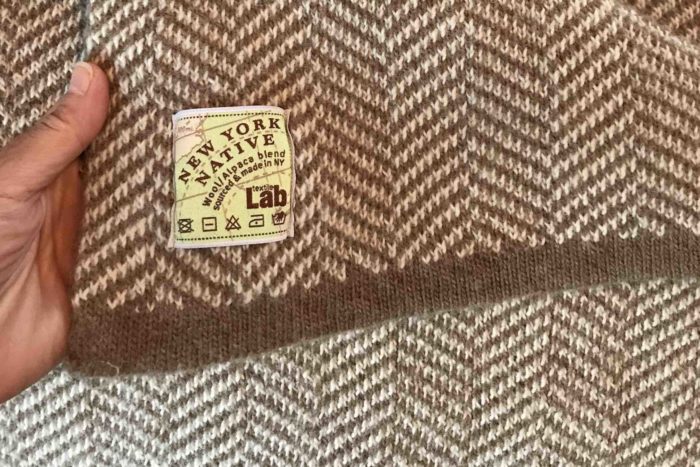
What is the criteria for the farms you partner with?
Since we’re developing machine grade yarns that are compatible with automated knitting machines and looms, we need to source fiber that is good quality to process and spin. We’re most interested in partnering with farms that can sell us larger quantities of fiber, approximately 100lbs or more, and the fiber needs to be about 3″ long for our industrial spinning needs. We’re also prioritizing colored fiber, designing the natural colors into the products we create. In the Northeast, we have a lot of Romney sheep breeds. This breed of sheep does well in the region unlike the finer wool breeds like Merino that thrive in drier climates. Although the Northeast breeds of sheep have coarser wool, we are able to develop textiles that are suitable for apparel applications by blending the wool with alpaca. We also have a lot of alpaca fiber here in NY and it really softens the hand of our coarser wools.
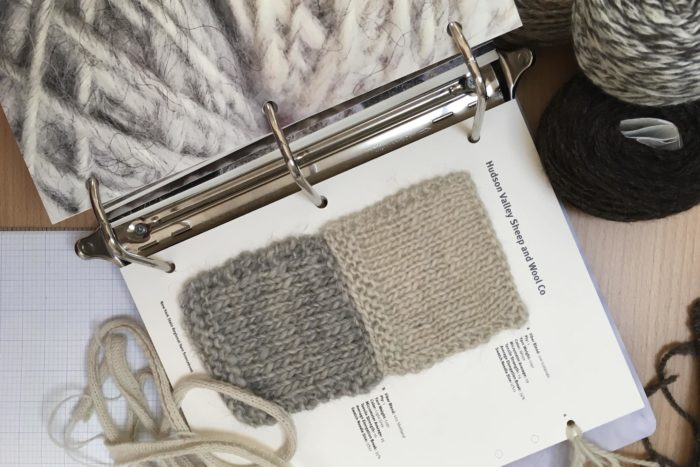
What is the difference between Nature’s Economy and our Industrial Economy?
Nature’s economy operates in circular systems. It grows fractally and laterally, promoting diversity and equilibrium. Nature’s economy doesn’t waste or deplete resources. It nourishes and regenerates. Nature’s economy is inherently resilient. By contrast, our industrial economy operates on a model of extraction, consumption and waste, which is linear. Our industrial economy intrinsically grows vertically, and it centralizes. This creates monopolies and a loss of diversity. As a result, our industrial economies are less adaptable during crisis. We saw breakdown in our industrial clothing systems during the Covid-19 pandemic. The textiles that are produced in China were delayed to the centralized manufacturing facilities in Bangladesh. As retail stores shut down across the world, many brands in the U.S. and Europe refused to pay for approximately 16 billion dollars in orders. As a result, thousands of Bangladeshi factory workers have lost their jobs or have seen a reduction in their wages. There are vulnerabilities in these large, centralized systems. Decentralized, bioregional economies are more resilient and support the well-being of natural systems and communities. This is why I focus on developing bioregional textiles.
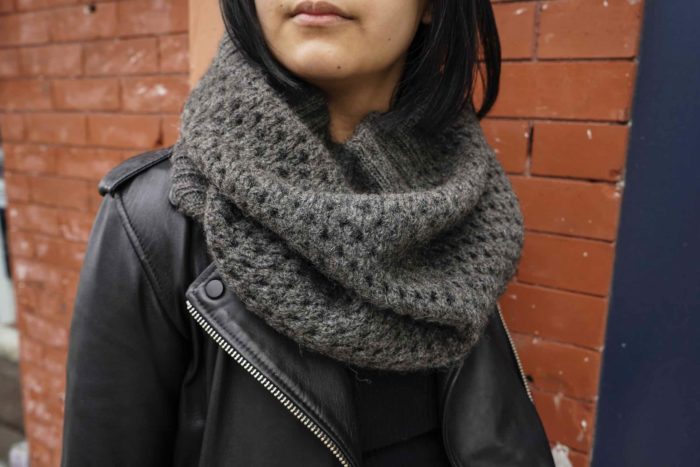
How viable are natural dyes on a large scale?
This is a great question and many designers ask this. Natural dyes are part of bioregional textile development. They reflect the capacities and limitations of particular ecosystems and are integral to place based design. This is because plants have particular growing ecologies and flourish in specific climates. There is an immense interest within the clothing and textile industry to scale natural dye production. As designers, we need to consider the growth logic of natural systems and remember the importance of biodiversity in the growing of our materials. This includes dye materials. It doesn’t make sense to try to accommodate large industrial systems if this means monocultured farming and depleting soil health. We’ll need to grow dye plants using regenerative farming models and carefully consider the provenance of the plants so there isn’t a disruption to bioregional ecosystems. The other consideration with natural dye applications is that naturally dyed products behave differently than chemically dyed clothing and textiles. Naturally dyed clothing is sensitive to certain laundering processes, and they need to be cared for more delicately. Although the colors and effects achieved with natural dyes are incredibly beautiful, natural dyes are less stable and more inconsistent than chemical dyes. These characteristics need to be communicated to consumers. Currently, there are a few production dyers in the U.S. who are scaling natural dyeing to a commercial level. Most of the production still remains at the quantity of small to mid-scale units to develop capsule collections for designers.
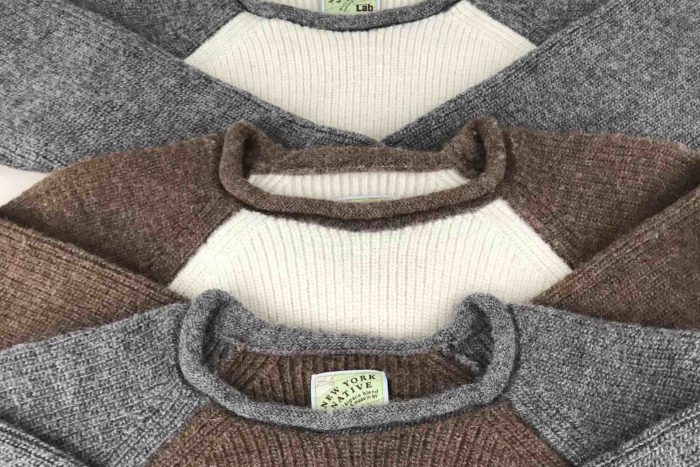
What is the philosophy behind Carbon Farm Plans?
This year we launched an application process for farms to join our Carbon Farm Network. This is an interconnected group of fiber producers who use climate beneficial practices on their farms, and climate-conscious textile and clothing designers who develop yarns and textile products from carbon-farmed fibers. I’m working with an Agricultural Planner named Gibson Durnford, who is affiliated with the Watershed Agricultural Council, to grow a Carbon Farm Network here in NY. I help to make connections between the designers, who want to use climate beneficial fibers and the farms who want to pursue Carbon Farm Plans (CFP’s) on their land. Our Ag Planner administers the CFP’s and conducts farm visits and soil tests. We’ve adapted AEM worksheets from the Natural Resources Conservation Service to use for our CFP application process. Our Agricultural Planner uses the USDA COMET accounting tool to understand the carbon draw down on the farms, and the climate beneficial fiber is verified through our affiliate organization, Fibershed.
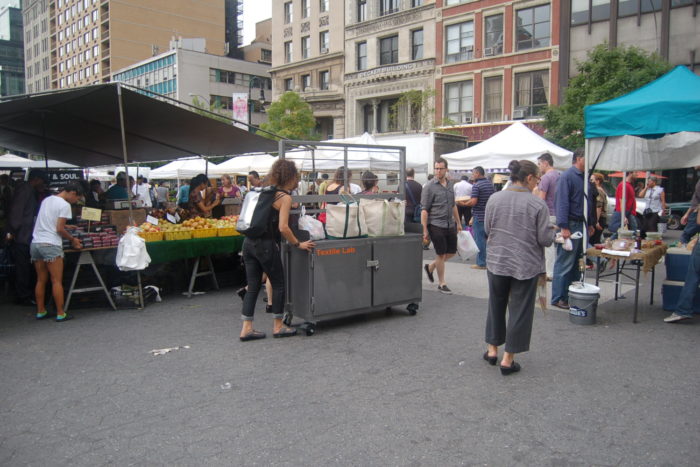
What are you most excited about in the design world at the moment?
I’m most excited about the post blockchain distributed network technologies that are emerging that can offer new ways to coordinate the activities within our textile supply network. There are platforms that are similar to blockchain, but unlike blockchain use a more scalable (and sustainable) structure enabling for a fractal, distributed growth logic much like the growth patterns we see in our natural systems. These technologies encourage patterns of social organization and will allow new economies to emerge around climate beneficial practices and ethical sourcing. I’m currently mapping an application using this platform to coordinate transactions between the agents (designers, farmers, mills) in our textile supply network, and resources (fiber). This technology will enable transparency making deep value flows visible like regenerative farming and localism. Our app will help independent designers connect directly to the other agents and resources in our region so they can design their own yarns starting with the soil where the fibers originate. The idea is that multiple stakeholders will benefit economically when we have a tool that enables our supply network to grow into a decentralized, diverse network.