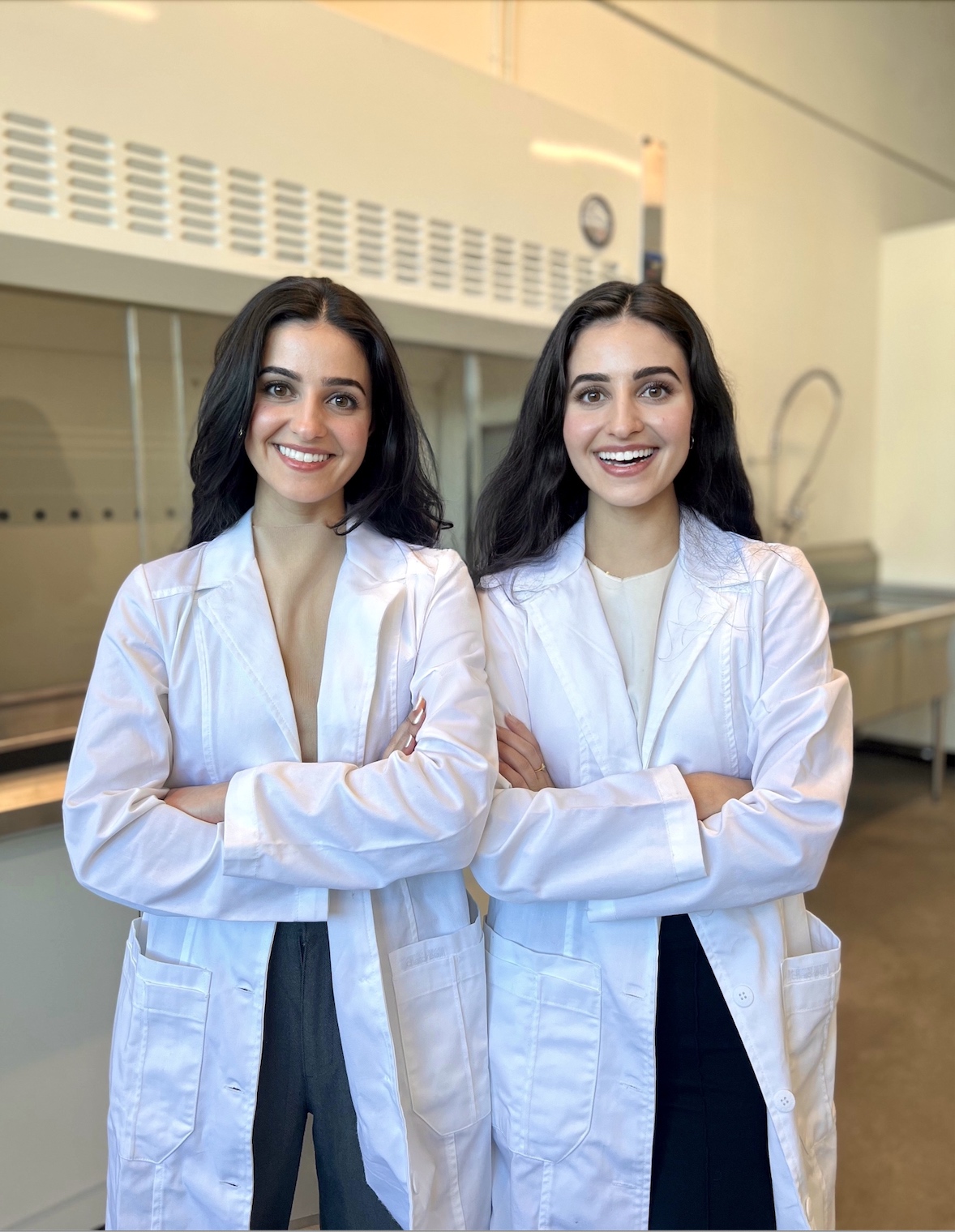
Scientists and twin sisters, Leila and Neeka Mashouf, are paving their own way in fashion though they’re no strangers to the industry (their uncle is Manny Mashouf, founder of Bebe Stores). Their upbringing—filled with learning from designers, manufacturers and more—was quickly followed by the understanding that our clothes come from some of the most harmful supply chains on Earth. The duo’s passion for bioengineering and environmental solutions led to working in a public biohacking lab until they invented and began prototyping for what’s now called Rubi Laboratories. The patent-pending technology behind Rubi converts CO2 emissions into carbon-negative textiles through a process called cell-free enzymatic biocatalysis. Leila Mashouf says, “It’s easy to conceptualize the process by thinking about the way trees grow. Trees breathe in CO2 and use it to build their trunks, branches and leaves. Just like how the enzymes present in plants power photosynthesis, we take the same approach to power our process with a cell-free system that, in turn, increases carbon utilization.” This week, the company announced its initial strategic pilot partnerships with Reformation, GANNI, Nuuly, H&M and Patagonia, as well as $8.7 million in Series Seed Funding ($13.5 million in total funding). They expect to begin releasing Rubi-based capsule collections later this year.
—Charlotte DeFazio
Where are you pulling the CO2 emissions from and how is it used to create your textiles?
Rubi uses biochemical processes powered by enzymes at an industrial scale to “eat” carbon emissions and make carbon-negative, resource-neutral textiles. Rubi’s cell-free biocatalysis process captures and converts CO2 from the waste streams of manufacturing facilities into cellulose pulp. Our technology is flexible on where the source of CO2 comes from, but ideally it’s from textile-related production like flue gas from a factory or industrial space. The converted cellulose is then used to create lyocell yarn which can be used for clothing and materials. 100% of CO2 inputted to the end product is done with zero waste.
What is cell-free enzymatic synthesis?
It’s easy to conceptualize the process by thinking about the way trees grow. Trees breathe in CO2 and use it to build their trunks, branches and leaves. Just like how the enzymes present in plants (called rubisco) power photosynthesis, we take the same approach to power our process with a cell-free system that, in turn, increases carbon utilization. To do this, we take an enzyme that grabs onto CO2 and breaks it apart, so another enzyme can then build carbon into cellulose. It’s the cellulose that we turn into the material that is used to make textiles, building materials, packaging and more.
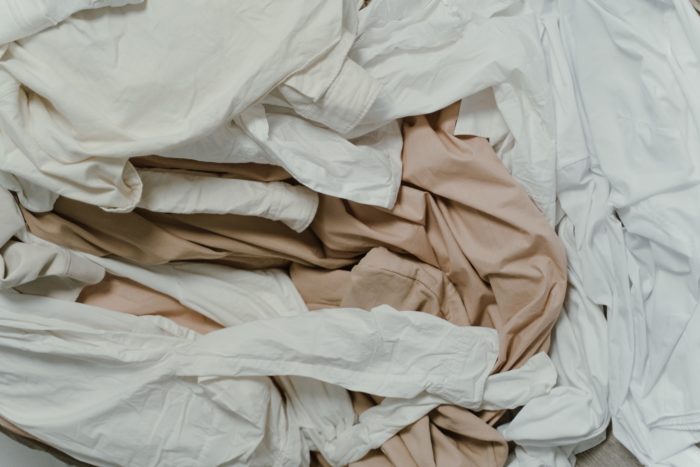
So far, how have you applied your textiles?
We’ve been working hard on our technology and have already produced fiber samples. We are entering pilot projects with various top-tier brands to make our product come to life.
Do you currently have a patent on your technology?
Yes, we have a PCT/Utility patent pending and several others in the pipeline.
You estimate that this process removes about two bathtubs of pure CO2 from the atmosphere. How did you come to that number?
That estimate is the volumetric amount of CO2 at standard atmospheric pressure that our process takes in to create material for an average pair of jeans.
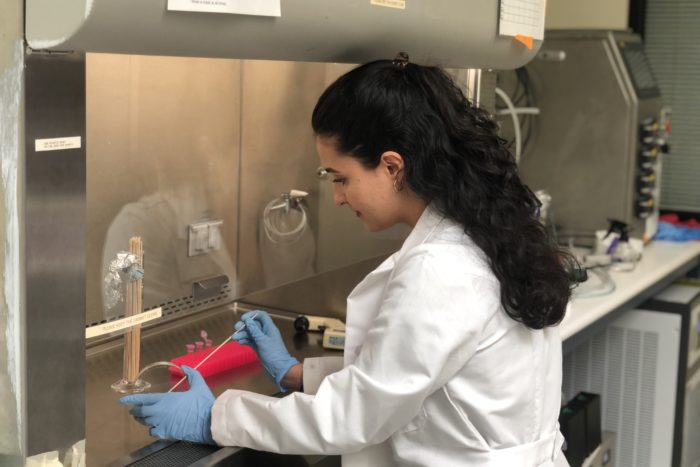
When do you expect to launch commercially? Have any brand partnerships been established?
We just announced our initial strategic pilot partnerships with global fashion brands GANNI, Reformation, and Nuuly including additional funding from Patagonia’s Tin Shed Ventures and H&M Group, among others. We’re in the process of finalizing additional partnerships and hope to continue building relationships with brands to make the biggest impact we can. While there’s still a lot to do before we can fully launch commercially, we’re excited to release capsule collections using our technology later this year.
Who or what has most influenced your work?
Ever since I was 15, I’ve been committed to understanding the biological systems that evolved to build carbon-based life. I wanted to take processes that happen in nature and apply them to solve real human-specific problems. After med school at Harvard, I realized the immense threat climate change poses, specifically in the fashion industry. Textile production is currently the third most CO2-polluting supply chain on the planet. The reality is that until there’s a way to produce sustainable clothing while also maintaining profit margins, we’ll stay where we are. Having family ties and a background in both the science and fashion worlds allowed us to see just how much progress can be made in sustainable fashion.
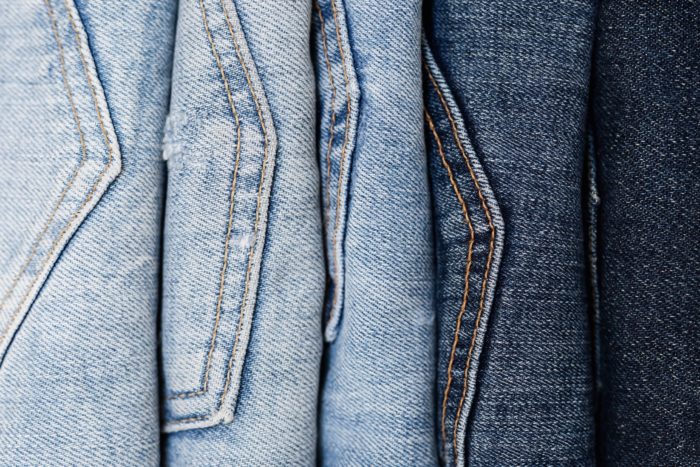
What’s next for Rubi Laboratories?
The company is just getting started and there’s a lot more in the pipeline as we continue to grow. Ultimately, Rubi’s technology has the potential to completely reinvent planet-positive global supply chains for materials like building materials, food, packaging and more. As we enter what I call the “symbiotic era,” Rubi will lead the way to create a world where human prosperity is planet-positive and global supply chains are symbiotic with the planet.